Comment Volkswagen a réduit ses coûts de production grâce à l'impression 3D
En 2014, le site Volkswagen portugais a investi dans 7 imprimantes 3D du fabricant néerlandais Ultimaker, afin de fabriquer lui-même des produits manufacturiers habituellement fournis par des prestataires extérieurs. À la clé, plus de souplesse, d'ergonomie et un gain de temps et d'argent.
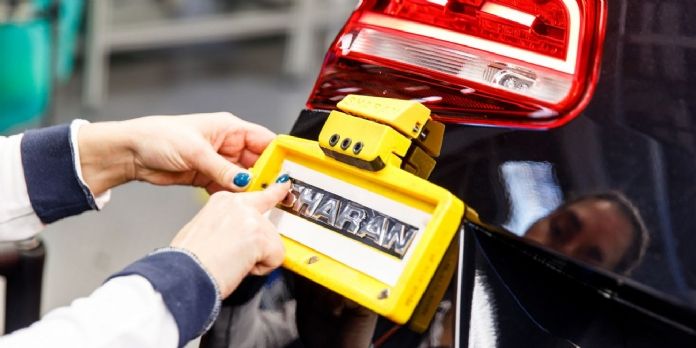
150 000 euros, c'est l'économie réalisée depuis 2014 par la filiale Portugal de Volkswagen Autoeuropa, qui a investi dans 7 imprimantes 3D Ultimaker. Grâce à cette technologie, le constructeur produit en interne environ 1000 produits manufacturiers destinés à des usages différents, calibres, gabarits ou encore supports pour la chaîne de montage. Autant d'objets qui ne sont pas commandés aux sous-traitants, entraînant de fait des gains de temps et d'argent.
Des outils plus ergonomiques
Mais surtout, l'impression 3D ouvre la voie à la création de designs complexes, sur mesure et en temps réel, en anticipant les problèmes potentiels et en modifiant à l'envi les moules, sans engager de coût. "Nous fabriquons surtout des outils d'aide à la production. Comme ils sont en plastique, ils pèsent moins lourd et sont plus maniables, tout en conservant un haut standard de qualité. Ces outils améliorent l'ergonomie donc la satisfaction et la productivité des opérateurs sur les chaînes de montage, se réjouit Miguel José, process engineer chez Volkswagen Autoeuropa, Usine Volkswagen au Portugal. Nous constatons un excellent niveau d'acceptation de la part des opérateurs depuis l'implémentation de cette technique".
Des cycles de production raccourcis
Ainsi, la conception d'un calibre destiné à placer les noms des modèles de voiture sur le hayon coûtait 206 euros en sous-traitance. Désormais, chaque calibre imprimé revient à 10 euros. "Les calibres sont plus simples et peuvent être constamment ajustés, contrairement aux modèles des fournisseurs externes", explique Miguel José. De plus, si le calibre imprimé est abîmé, il suffit de remplacer les parties endommagées, là où auparavant, l'outil était carrément jeté. En termes de temps, la réalisation du projet passe de 35 jours à 4 en moyenne.
Des résultats incontestables
De l'idée au prototype, Volkswagen consacre désormais 1h à 1h30 pour un projet simple, plutôt que 2 à 3 semaines. En se passant de ses fournisseurs et des délais inhérents à la négociation, les délais sont réduits d'en moyenne 8 semaines. Ainsi la transition vers l'impression 3D a permis à Volkswagen de réduire ses coûts de développement de 91% (comparé à l'externalisation vers des fournisseurs), de réduire les délais de développement de 95% (en deux ans ils sont passés de 70 à 95%) et de réaliser une économie globale de 150 000 euros. Les imprimantes ont été rentabilisées en deux mois.
Volkswagen envisage de monter ses économies à 250 000 euros par an et espère atteindre 320 000 euros à la fin 2017. "Nous utilisons un produit abordable qui produit des résultats haut de gamme. Si l'on prend en compte toute l'industrie automobile, il y a un fort potentiel", confie Miguel José. En effet, avec des imprimantes coûtant entre 3 et 4000 euros chacune et un logiciel gratuit en open source, Ultimaker Cura, "notre technologie est très accessible pour un usage professionnel, alors qu'elle a moins de 10 ans", rappelle Paul Heiden, senior vice president product management chez Ultimaker. L'impression 3D favorise les itérations et accélère de fait le lean. "Les entreprises commencent à changer de mentalité et l'utilisation de l'impression 3D explose dans des secteurs aussi variés que l'industrie ou le médical. Et son taux d'adoption est à chaque fois extrêmement rapide", conclut Paul Heiden.
À lire aussi:
Sur le même thème
Voir tous les articles Autres Achats